Understanding Standard Methods of Testing for Rigid Packaging
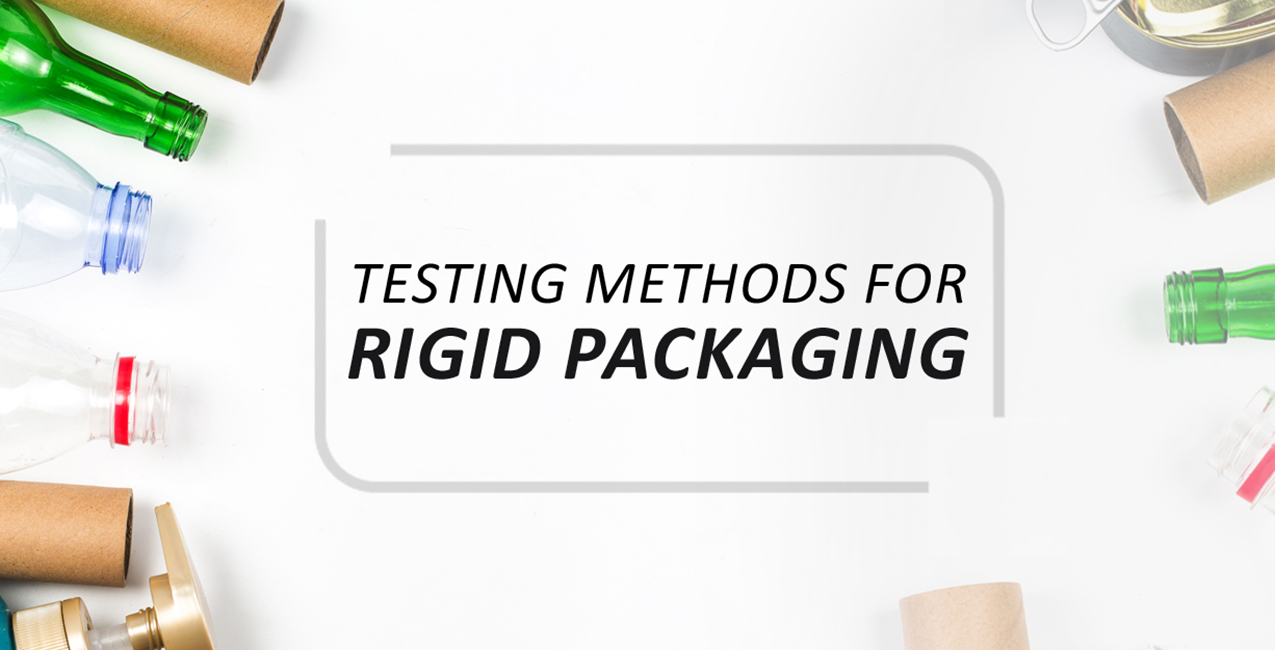
Completion of design and development of packaging seems like the end of the significant tasks. But does the work really finish up with that? No, it doesn’t. Next up is testing.
Testing is a very crucial part of the entire packaging cycle and implementation of appropriate procedures is critical to make sure that the package developed is catering to all the requirements. It gives an idea of what sort of stress that packaging will be able to endure during the shipping as well as during the packaging process in the assembly line.
Now, when we speak of testing, rigid packaging is something that needs extra care. Rigid packaging consists chiefly of hard plastic jars and bottles, aerosol bottles, aluminium bottles, glass jars and more. Even amongst these, rigid plastics make up a large share of packaging and containers. They are used in the food industry, the pharmaceuticals, as well as for a wide range of other products, such as cosmetics or stationery. Rigid packaging often comes in multiple parts – the caps and containers are separately manufactured.
Therefore, the testing for rigid packaging can be divided into two sections: Testing for individual components and testing for individual packaging. Here are some of the testing for rigid packaging methodologies categorized as per the ways of testing.
Complete Testing for Rigid Packaging
This section deals with the packaging testing methods applied to the entire packaging. These include the dimension testing, crack resistance testing, drop testing and more.
1. Dimension Testing
The need for testing the dimensions arises from the need to be bundled properly and the ability to be filled and labeled using an automated assembly line. The height, width, length, or diameter of the product is tested. The weight is also often tested. However, assembly lines have very precise machinery that may not work if the bottles or jars are of different sizes. Moreover, while labeling or sealing, the correct dimensions ensure that the automated processes can take place without any errors.
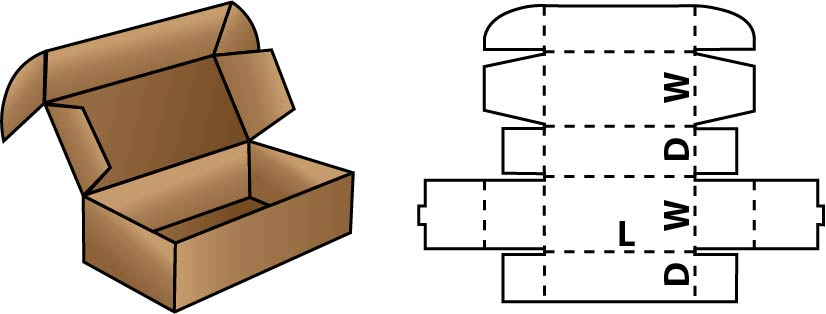
2. Overfill Capacity Testing
Closely related to the dimensions is the overfill capacity. Overfill capacity is the capacity of the bottle or jar when filled up to the brim. This allows the manufacturers to determine if certain types of products will fill in certain types of bottles.
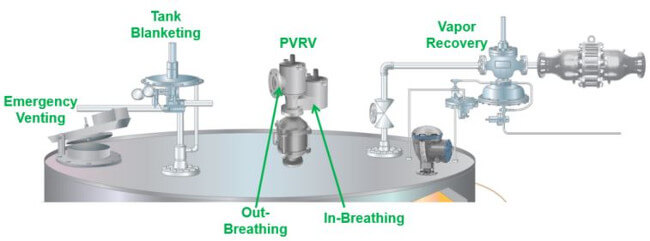
3. Environmental Stress Crack Resistance Test (ESCR)
Environmental Stress Crack Resistance or ESCR Testing is a quite common test for plastic bottles. Rigid thermoplastic bottles often fall victim to Environmental Stress Cracks. Pet bottles, over time, become brittle when exposed to the weather. Plastics undergo polymer degradation over time. This breaks down the secondary linkages in the polymer molecules. A plastic container that has undergone such degradation will often crack when exposed to any form of external mechanical forces. ESCR testing for rigid packaging allows manufacturers to see the effect of polymer degradation on containers and how much stress the container can handle after a long shelf life.
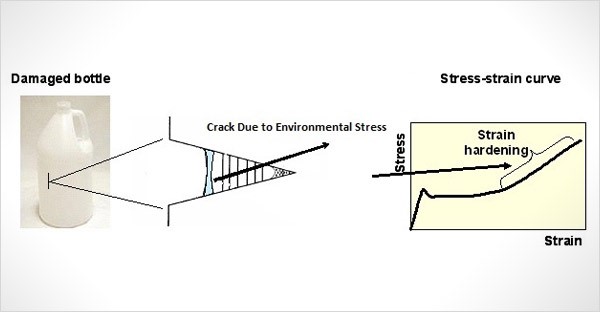
4. Drop Tests
This check if the container can sustain drops when filled with the product. Drop tests have certain standards where the package, filled with the product is dropped on a hard surface from certain heights.
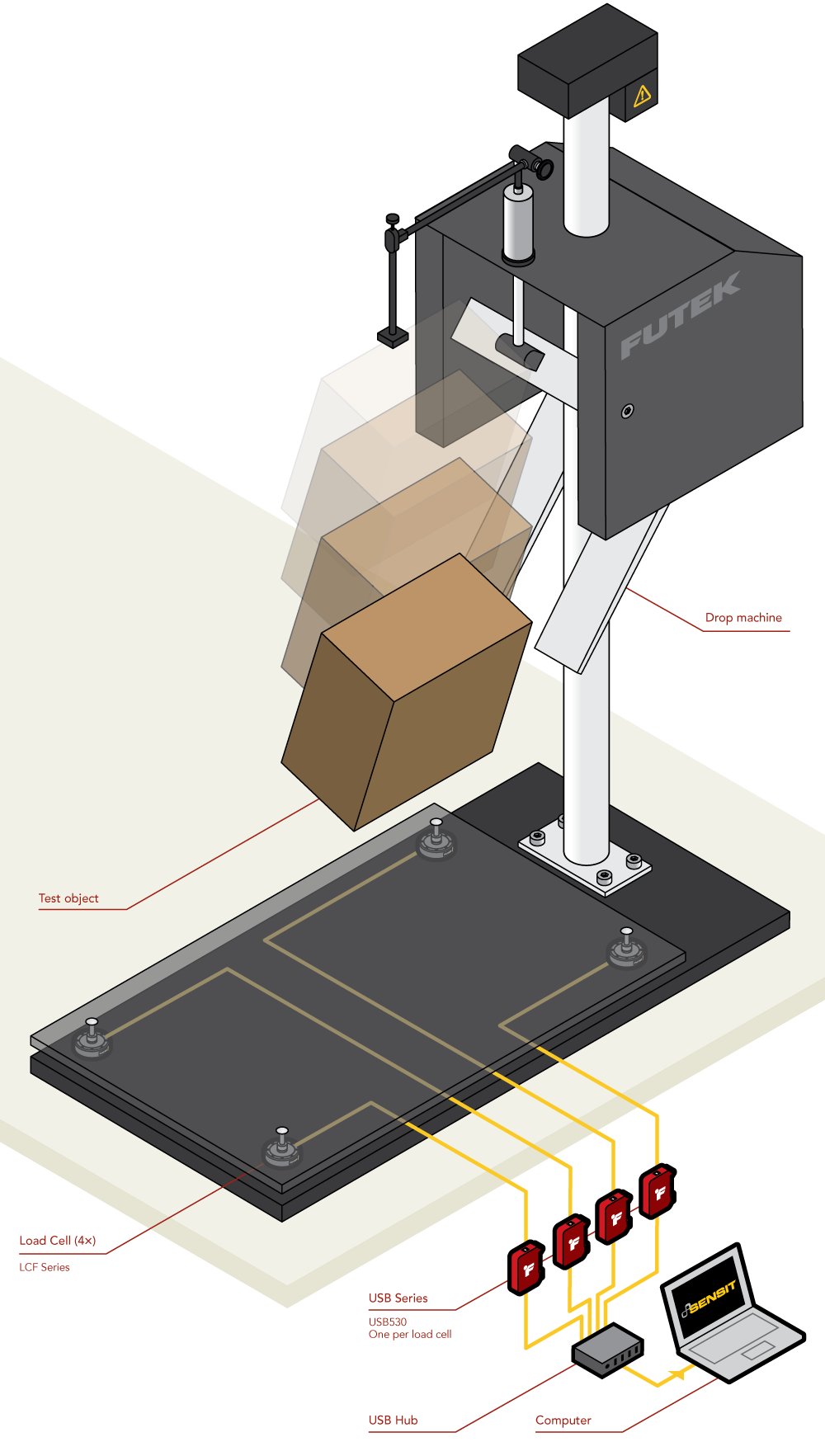
5. Leakage Tests
Leakage tests allow manufacturers to see if the container can hold the product under different pressures or under different orientation. It is one of the important considerations in packaging material testing methods. Leakage tests are generally divided into two parts – vacuum leakage and slant leakage.
In case of testing vacuum leakage, the container, with the product is put in a vacuum sealed chamber and the pressure inside the chamber is dropped. If improperly manufactured, the walls of the packaging or the region of the seal will begin to leak. The slant leakage test checks different orientations of the package for leakage.
6. Transit Tests
Transit tests check how much stress the packaging can endure while it is being shipped in bundles. The packaging is subjected to different types of stresses when it is out on the road, being transported from point A to B. These stresses are much different from those that the packaging will face in retail stores or when it is with the end user. Transit tests check how many drops, how much inclination or vibration the packaging can endure.
Individual Component Testing
Packaging test standards appreciate testing the individual components of the packaging. Individual component testing checks the caps and closures. These include the hinges, the locking mechanisms as well as the materials they are made out of. Here are some of the tests that are performed on the caps and closures.
1. Cap Fitment
This test ensures that the cap properly fits on the top of the container and does not cause any leakage.
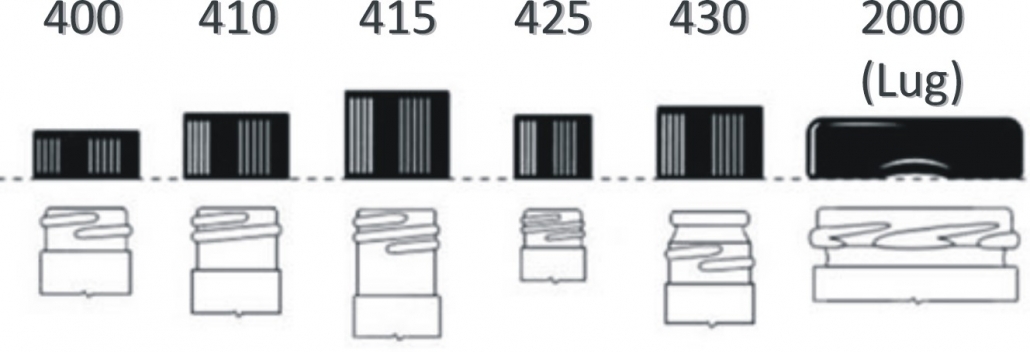
2. Top Load Testing / Compression Testing
Top load testing for rigid packaging or compression testing checks how much load the closure can take before it breaks. This testing for rigid packaging is essential because while shipping the jar and bottles are stacked on top of each other. The Top Load Testing or Compression Testing gives an idea of how many bundles it is possible to stack.
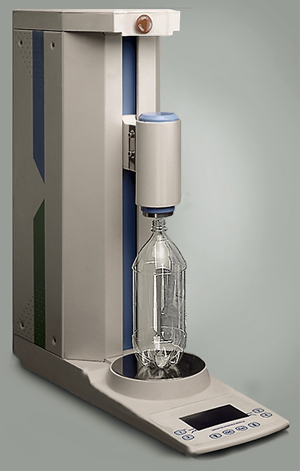
3. Hinge Performance Test
For closures that come with a hinge mechanism, the hinge performance tests examine how much force the hinge can take as well as how durable it is, that is, how many times the hinge can be opened or closed before the hinge breaks down.
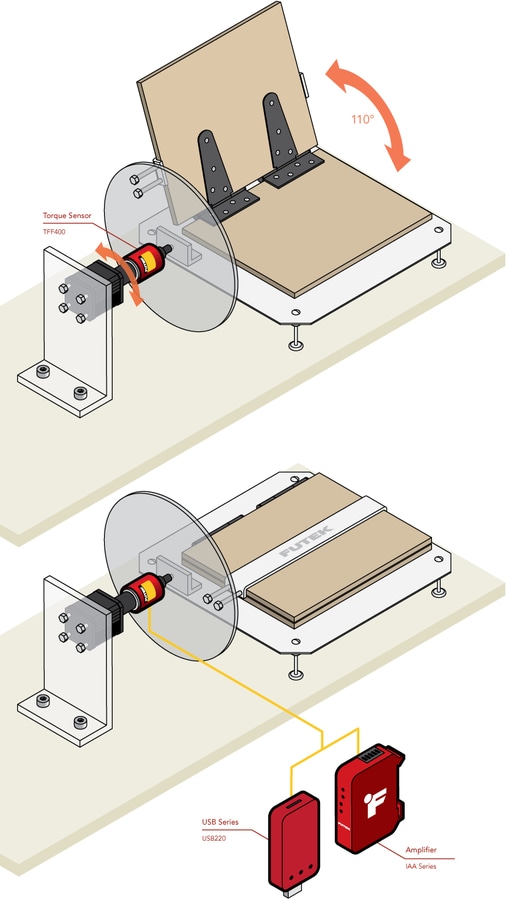
4. Flip Top Opening Force
In flip top caps, common with ketchup bottles, the flip top opening force determines how much force is needed to open the cap. If the flip top opening force is too high, then opening the cap will also break the hinge.
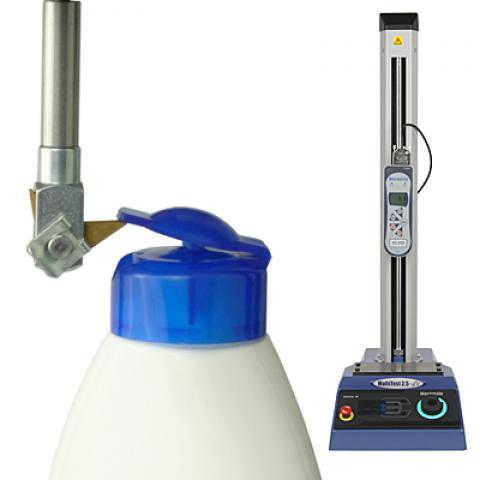
5. Cap Removal Force
The cap removal force should be more than the flip top opening force. This ensures that the cap remains snugly on top of the container.
.jpeg)
6. Torque Test
This test checks if the cap can handle the shearing force that is needed to open or close the cap. This is primarily tested for caps that use a screw mechanism for opening and closing. Apart from rigid packaging, what other materials are available in the market, you can read here.
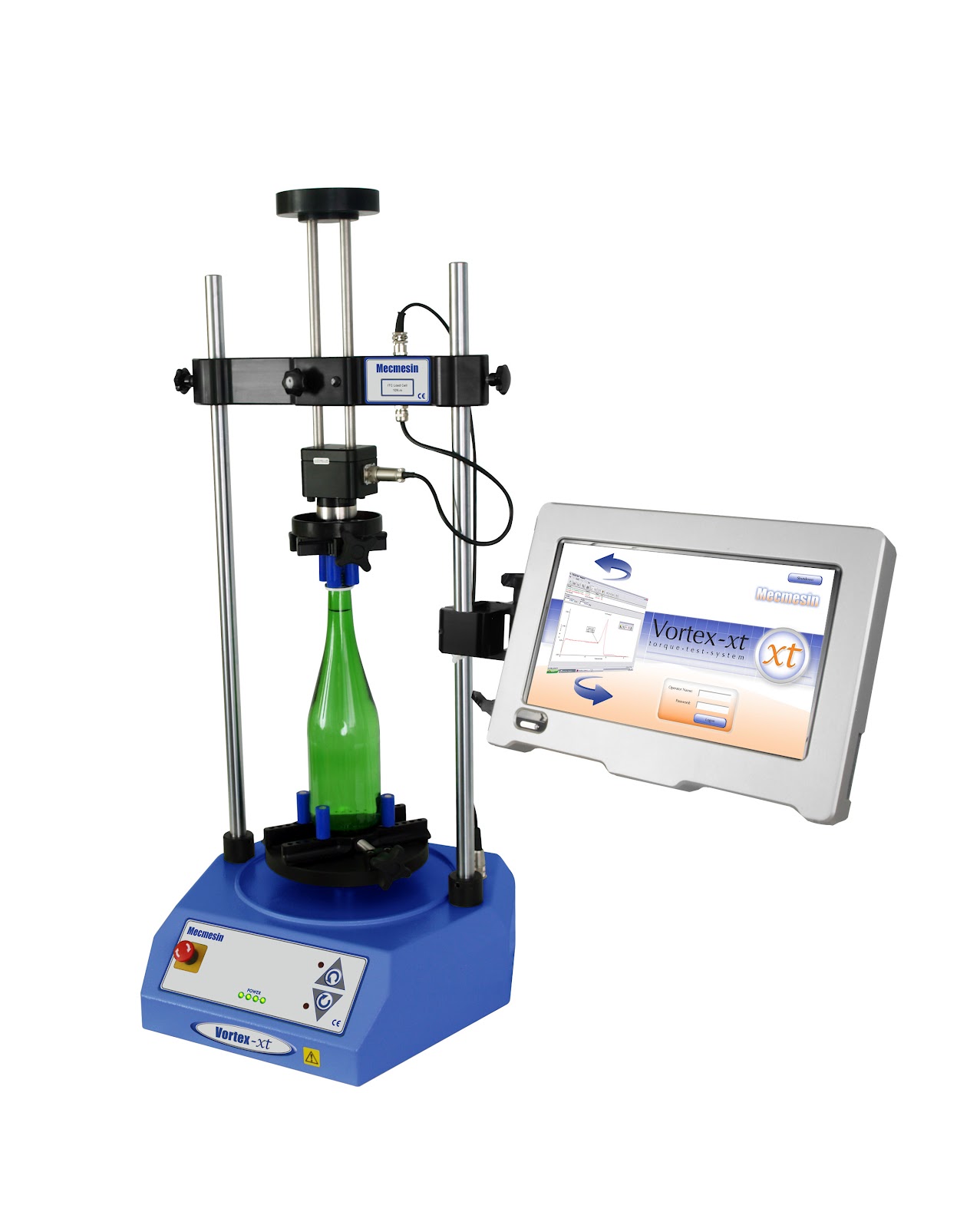
Alternatively, if you are using flexible packaging, read: Testing Methods for Flexible Packaging
Bottom-line
Besides these, there are tons of other standard testing strategies for specific rigid containers. Manufacturers use these tests to determine the durability and life of the packaging. Rigid containers not just help manufacturers deliver the products to the consumers, they also stay a significant amount of time with the consumers. Hence, a quality control test for plastic containers is quite essential.
Still confused which is better among rigid and flexible packaging for your business? Read up to get the answer.