Why Does Your Commercial Warehouse Flooring Need a Makeover?
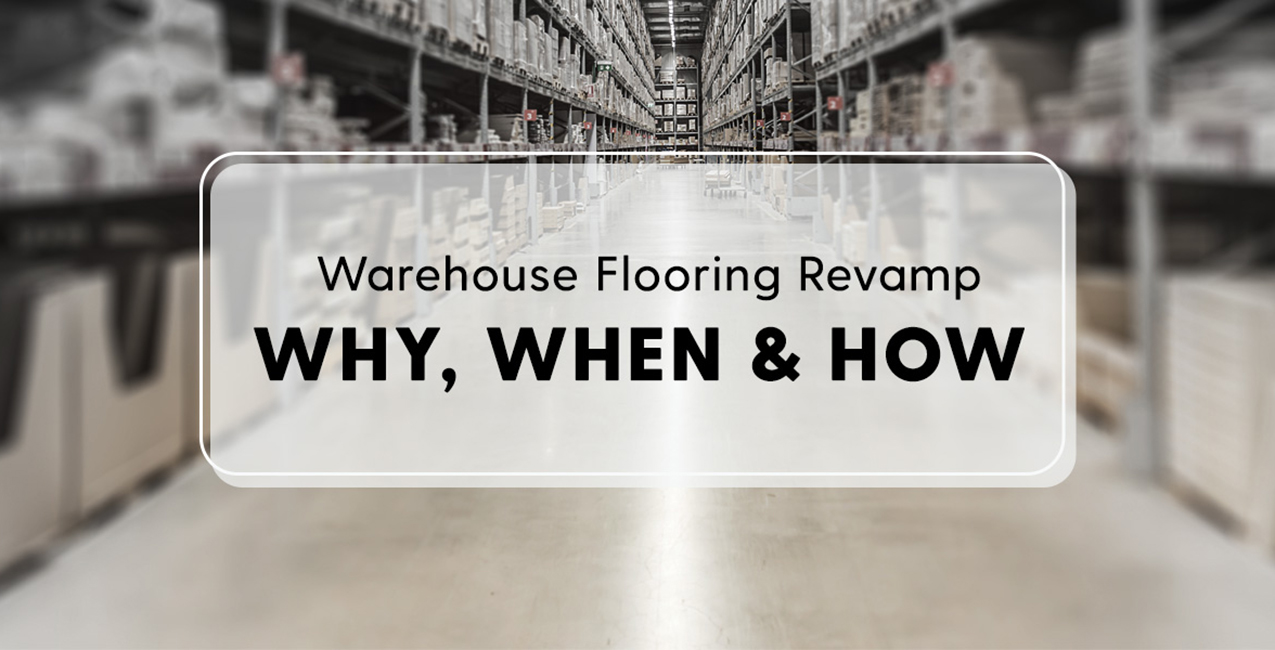
Warehouse flooring is different from any other types of commercial flooring. A warehouse floor is abused much more than any other types of commercial flooring. Every single day, a warehouse is likely to have a lot of forklifts and pallet trucks moving around. Sometimes, heavy loads are also dragged around in the warehouse. Scuffs and scratches are quite common in warehouse floors. Moreover, warehouse floors also have to take massive weights. However, warehouses also need to be presentable for business tours for clients and customers. Besides being presentable, commercial warehouse flooring also directly determines workplace productivity and safety.
Reasons for Wear and Tear of Commercial Warehouse Flooring
Most warehouses have concrete flooring. Sometimes, they also have decorative layers on top of concrete flooring. These floorings get damaged over time because of the heavy traffic in a warehouse. Forklifts or other vehicles create tire marks on the flooring that does not easily go away. Flooring can get scratches from loaded pallets being pushed around. Floors can also get damaged if heavy loads fall on the floor, or if there is spillage of any kind of corrosive chemicals.
Signs When the Flooring Needs Repair
Here are some of the common signs of worn out warehouse flooring that need reworks:
- Gouges and scratches: Warehouse floors are first dulled by gouges and scratches. These happen when heavy loads are dragged over the floor. Rough or damaged pallets or other uneven loading surfaces, as well as badly operated forklifts, can cause such scratches. Concrete floors get scratched quite easily since their surface hardness is not very high. However, repairing these are also easy. The concrete surface can be polished and restored quite easily.
- Tire mark stains: Tire marks stains happen when a lot of forklifts or pallet jacks operate in the warehouse. Tire marks happen either from worn-out tires or when the vehicles skid on the smooth concrete surface. Tire marks are not very easy to get rid of. They need abrasive chemical treatment.
- Reduced Floor flatness: Reduced floor flatness happens when the foundation of the warehouse itself is not strong. Often, a warehouse with a weak foundation will result in a low spot where loads are kept. For leveling the floor, the existing flooring needs to be completely removed or redone.
- Floor cracks: Reduced floor flatness is often accompanied by floor cracks. Minor cracks can be filled with cement mixtures, but larger cracks need elaborate repair work. Cracks may also happen when something heavy falls on the floor and the floor surface could not withstand the impact.
- Chemical wear: Corrosive chemicals such can concentrated acids may leave permanent marks on concrete flooring.
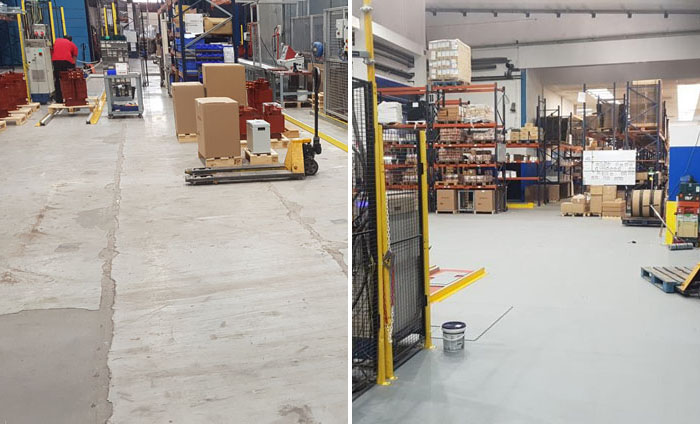
Consequences of Bad Flooring
Your bad commercial warehouse flooring can not only reduce productivity but can also increase operating costs and can even be a safety hazard. Here are some of the common consequences of bad flooring.
- Lift truck damage: Lift trucks and forklifts mostly use cushion tires that are not meant for rough surfaces. Only a few models make use of pneumatic tires. Rubber tires wear out pretty quickly when they run over holes and cracks. Moreover, bumps can also increase the risk of loads falling over. The trucks may also need to take a separate route if a part of the flooring is damaged too badly.
- Vehicle operator fatigue: Bad floors also causes vehicle operator fatigue. Operating a lift truck of a forklift in tight spaces can be quite difficult and require a lot of mental resources. With defective flooring, the task of operators become a whole lot more difficult and increases the chances of accidents.
- Reduced productivity: Bad flooring can slow down the movement of goods in the warehouse. It can result in vehicle damage, increased downtime, and reduced material handling productivity
- Increased housekeeping costs and bad sanitation: cracks and crevasses can collect dirt and dust can be hard to clean out. Often, they can be breeding grounds for mold or can be an entry point for rodents.
Also read about the packaging challenges at warehouses.
Standard Repair Procedures
Repair procedures and the time required for them depend upon the damage that the flooring has faced. For instance, simple crack repairs can be done quite quickly. Presently, epoxy injections are used to fill in the cracks that harden pretty fast. Similar epoxy based patching material can also be used to fix dents and holes in the flooring. However, none of these quick-fix methods are long lasting as standard repair procedures that address the problem right at the root.
- Concrete Floor Joint Repairs: Joint repairs are a simple procedure where the damaged area is cut out and is filled with concrete or any other bonding agent to create a smooth leveled surface. In case of small repairs, there is almost no downtime and the warehouse can remain operational while the repair work is being carried out.
- Lifting and Leveling Concrete with Polyurethane: Uneven or sloped floors can be leveled using polyurethane foam. Pipes, wiring, and rebar embedded in the concrete are first mapped out to prevent any damage. Then the voids are filled with the foam to level the concrete.
- Decorative Coatings for Concrete Floors: Commercial warehouse flooring does not always have to be bland. They can be covered with durable and colorful tiles, or can be coated to enhance the aesthetics and also improve the strength. These can prevent scratches or tire marks.
How to Prevent Warehouse Flooring Damage
Commercial warehouse flooring repairs can be time-consuming and the downtime can affect your business. Hence, simple regular maintenance can help prevent premature damage to warehouse flooring. Here are some of the things that one should look after to ensure that the warehouse flooring stays in good shape:
- Clean dust and debris: Loose nails, nuts, and bolts, or even dirt can affect the commercial warehouse flooring. When heavy machinery moves over these, they can get embedded deep in the flooring and cause cracks. Hence, cleaning the flooring once a week or so, and being aware of any small loose metal parts lying around on the flooring can help prevent damage.
Read: How to sanitize the warehouse?
- Check forklifts, lift trucks and other vehicles: Tires on the forklift or lift trucks that are worn out can cause damage to the flooring. Tire marks are common when you have worn out tires. Similarly, you need to check pallet jacks and other vehicles that operate in your warehouse.
- Rethink the layout: The warehouse floor plan can be changed to uncover parts of the floor that stays covered with the load all the time. This ensures that all parts of the warehouse floor get cleaned. You can also go for standard industrial flooring materials instead of local ones.
- Invest in professional cleaning: Having the facility cleaned and scrubbed a few times every year can be quite cheaper than making expensive repairs. A deep clean allows you to detect early signs of damage and even prevent some. Besides regular in-house cleaning, having a dedicated team to clean your floor can actually help you save on repair costs.
Conclusion
When it comes to commercial warehouse flooring, prevention is better than cure. From the inception of your warehouse, invest in industrial flooring types. Using smaller concrete slabs can reduce the chances of cracks in the flooring resulting from shrinkage. Moreover, after a repair, or a rework, it is best to avoid work for fourteen days. That is the time needed by concrete to reach its optimum strength. Furthermore, smaller cracks or scratches should be repaired as they appear. Delaying repairs can end up costing a lot more.
READ: Expert reveals answers to 5 FAQs on warehouse logistics.