7 Easy Ways to Reduce Packaging Inventory Replenishment Costs
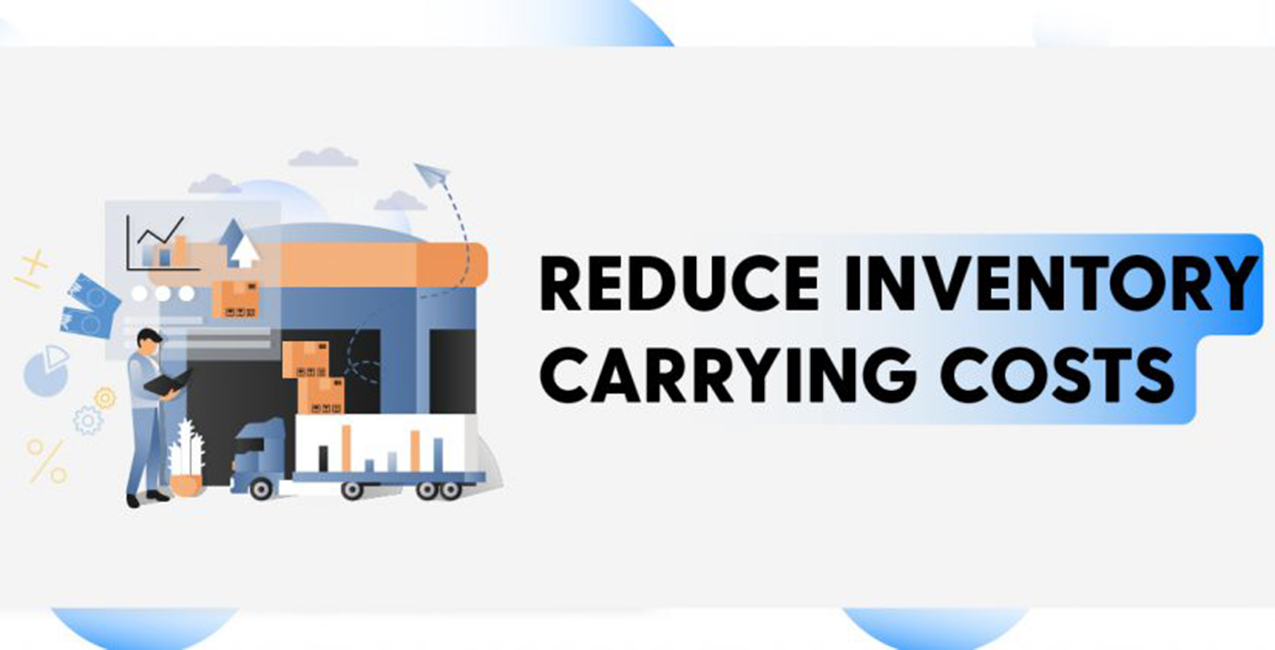
Cost plays an important role in determining the sustainability of operations for any company. By cutting down on the inventory replenishment cost, businesses save time and money. In turn, they can prevent packaging stock-out.
7 Methods to Optimize Inventory Replenishment Costs
1. Organize Warehouse Storage
Expanding the warehouse space can be a costly affair, therefore it is better to find ways in which the existing warehouse space can be utilized efficiently. Accurate demand forecasting is necessary to understand how much stock and packaging inventory needs to be ordered. This will help you in allotting the storage space precisely.
Systematize and compartmentalize your inventory carefully. Try to place high-demand goods upfront so they are easily accessible. And keep an option of adding more aisles if your inventory need is going to increase.
2. Keep Track of Inventory Levels
Be it stock or ordering for packaging materials, it is better to keep track of inventory consumption in order to know when replenishment will be required. This way you can prevent delays in delivering orders to customers and save cost on ordering on an urgent basis.
Deploying software that keeps a tab on your inventory status in real-time can help you know the exact reorder point so you can be assured and prepare in advance.
3. Dispose Off Obsolete Stock
It is always a possibility that obsolete stock is lying around in your warehouse and eating up space that could have been used to store essential stock or material. Find a way to sell or recycle the unused inventory.
Get a system in place to record the inventory so you can be alerted when any goods in your inventory are lying unused for a long duration. By knowing how much you require, you can save costs on material procurement and also optimize the warehouse space.
4. Work on Reducing Order Lead Time
Lead time usually depends on how big your order is, hence, making small and frequent orders can significantly reduce it. Combine orders of items that sell together or switch to open purchase orders.
By partnering with sellers who provide the option of open POs and replenishing the inventory as it is consumed, not only can you reduce lead time but also eliminate the risk of overstocking.
Another way of reducing lead time is by switching to local suppliers. Set a quality standard for your goods and source them from suppliers that offer the shortest possible lead time.
5. Audit Workflow Regularly
All aspects of a business need to be audited regularly. As market volatility modifies, a need to change these processes will arise. Set standards in the workflow which all the employees can adhere to, and maximize their efficiency. Revisit the standards to make amends or to adapt to prevailing demands.
6. Switch to Automated Processes
Automation has made its mark in the market from simplifying processes to eliminating time-consuming steps. Automation software can make managing your inventory smoother.
A cloud-based inventory management software will help you know your reorder point, keep track of the unused inventory and alert you in the reversed situation. It will also help in streamlining the processes and reduce dependency on forecasting.
7. Reduce Reverse Logistics
Returns and repairs are unavoidable in any business, but they can be minimized. Two factors that can help are maintaining quality and communicating clearly with the supplier. Regularly generate quality reports and fix on product quality with the supplier after seeing the samples.
Communicate your specifications in detail, and use technologies like 3D printing to understand the exact quality of the packaging material. Ask the supplier to send a quality certificate along with the inventory. You can also opt for reusable or recyclable materials to reduce cost in case of return.
Final Thoughts
Saving inventory replenishment costs is easier with the right software and partners. A partner that allows you transparency of processes and ease of operations can help you be more efficient money-wise and in terms of logistics.
For best results, evaluate your requirements and chose a software or a partner that can work exactly as per your requirements, give you the charge of operations and leave the uncertainty behind!